Flexographic Printing Explained
Flexographic Printing Process:
Flexography is a form of rotary printing that transfers ink from flexible plates mounted on rotating cylinders to substrates. The process is known for its fast printing speeds, ability to print on non-flat surfaces, and the use of fast-drying inks.
Ink Transfer:
In flexography, ink is applied to a plate with raised images and text. The plate is attached to a cylinder, making contact with the substrate as it passes through the press.
Inks and Colors: The type of ink used (water-based or UV-based) affects the drying time and durability. The color choice impacts the vibrancy and appeal of the final product.
Plate Making:
The printing plate is created from a digital image. This plate carries the image to be printed and is crucial for detail and clarity.
Artwork Design: The complexity of the design and number of print colors dictate the plate-making process, affecting resolution and print quality.
Printing Process:
The substrate is fed through the press, where each color is applied by a separate print station. The final number of colors or finishes determines the number of passes and stations used – our presses have from six to eight print stations.
Substrate and Adhesive Types: Different substrates and adhesives are chosen based on the application surface type and conditions, impacting adhesion, appearance, and performance.
Drying and Curing:
After the ink is applied, it must dry or cure. UV inks cure instantly under UV light, while water-based inks may require additional drying time.
Application Conditions: Environmental factors, like humidity and temperature, can affect ink drying and adhesion, influencing the choice of inks and drying methods.
Cutting and Finishing:
Once printed, the labels are cut into their final shape and size, often using a die. Special effects like foiling, reverse prints or laminates are applied in subsequent stages.
Die Shapes and Special Effects: The chosen size and shape, as well as any additional finishes like varnishes or holographic effects, add to the label’s functionality and aesthetic appeal.
Variables Impacting Flexographic Printing:
Label Size (Dimension):
Determines the plate size and the press setup, impacting cost and waste.
Quantity Required:
Influences the production run length and potential economies of scale.
Number of Variants:
Affects the number of plate changes and setup time, influencing turnaround time.
Substrate Type:
Dictates the ink types and press settings, affecting print quality and durability.
Adhesive Required:
Influences label performance, particularly its ability to stick to the application surface.
Application Surface Type:
Determines the compatibility of the label with the intended surface.
Application Conditions:
Environmental factors can affect label application and performance.
Number of Print Colors or Design:
Impacts the number of plates and print stations needed, as well as the complexity and cost of the print job.

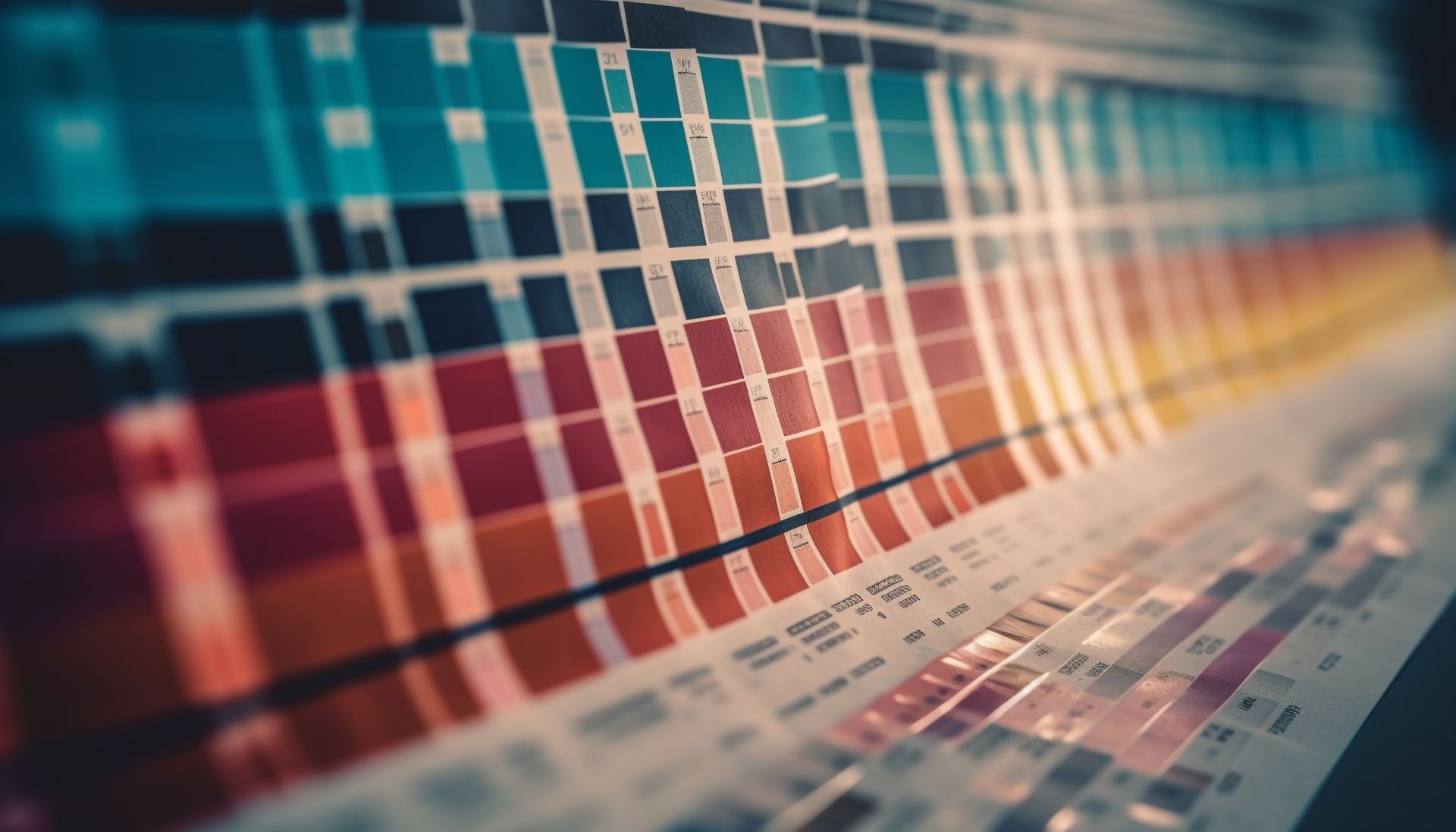
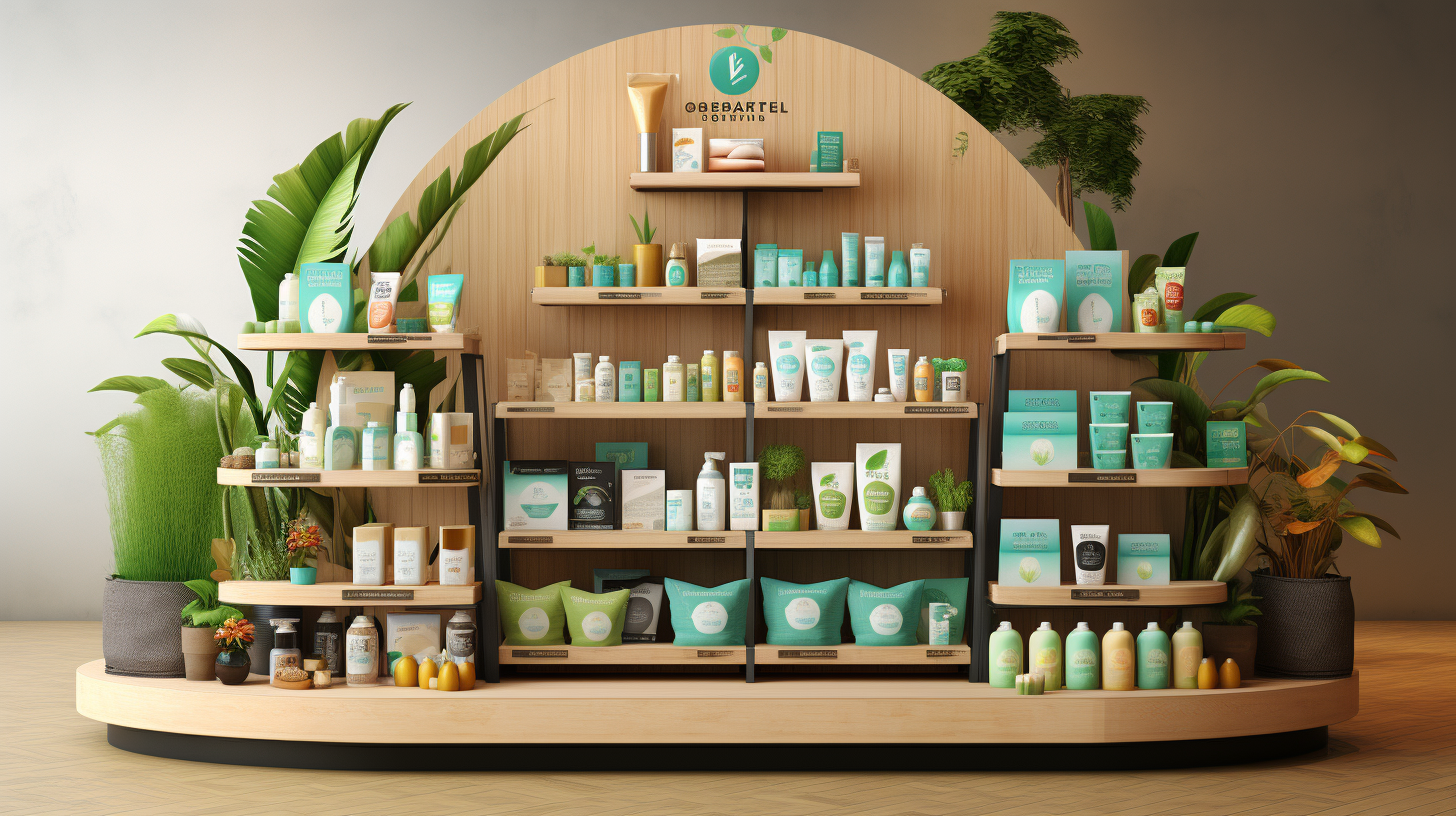

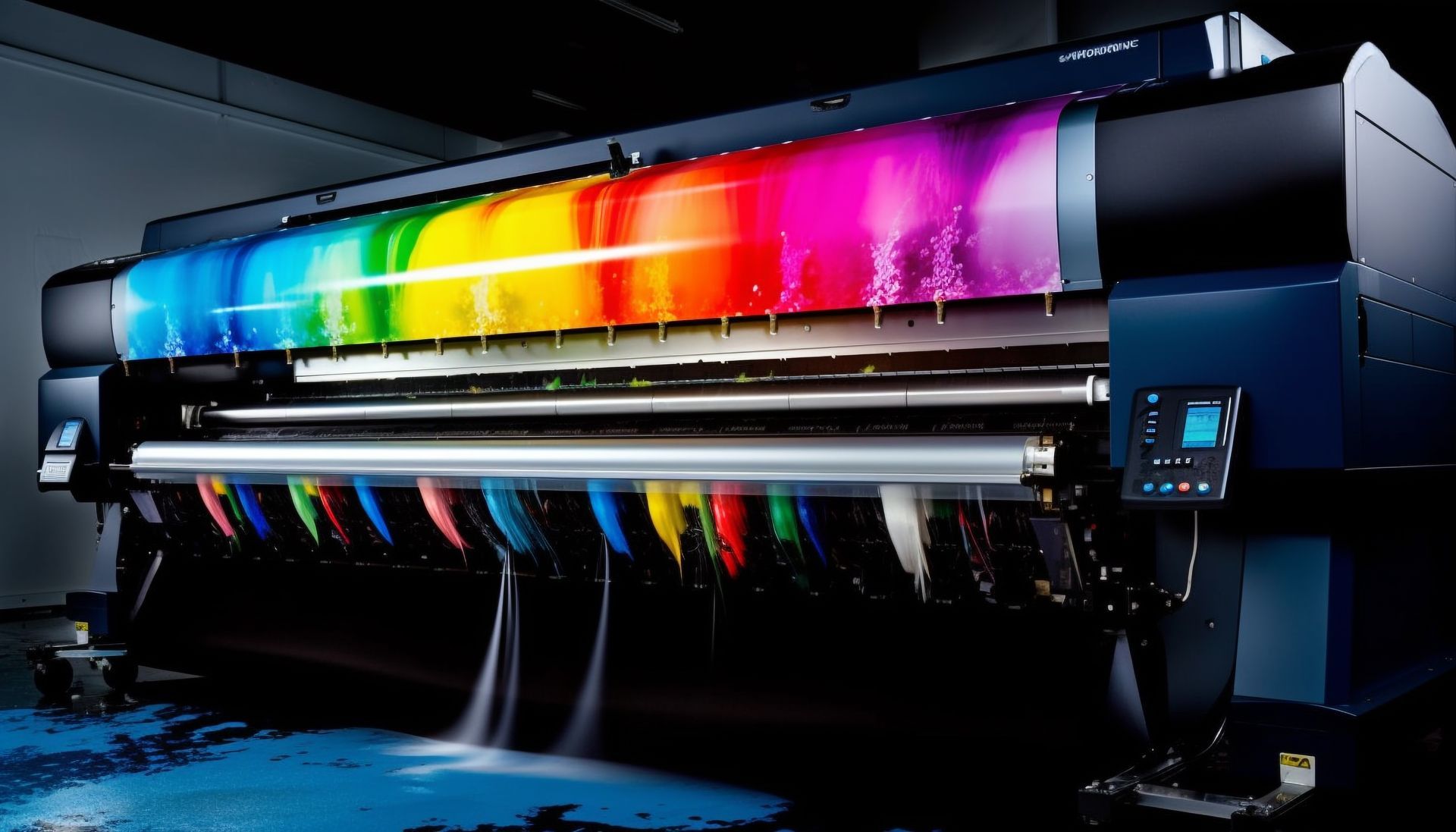

